...are you talking about boolean on a high level mesh..........dave
Yes.
A very common technique I see used in the modo and lightwave forums is to build the base mesh, then smooth to a higher level of detail and freeze the mesh and then trim out the higher level detail parts like hatches and openings.
I constantly struggle to find better ways to put openings into surfaces, especially ones with tight corners, without getting seems, pinching, and lump and bumps into the nice surface I have worked so hard to get as close to G3 as possible.
It seems smoothing and then cutting openings and panels reduces the need to run diagonal edges all over the lower level mesh in an attempt to spread edges that radiate out from tightened corners.
In most examples I have seen a cutter object is created and the openings are booleaned out. Lightwave also has the stencil which is projected on to a surface and can act as a cutter, similar to projecting curves on a maya nurbs surface and then trimming.
Here are some wires of the low res mesh which is at around 34000 polys - 31000 of which are in the engine. Each engine component is very low poly, there are just a lot of components. The engine could have a lot more components but I added only as much detail as needed to get a fairly convincing medium to close shot.
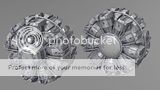
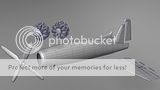
This is an entire area of training that I find missing in all the 3D forums I have read - techniques for creating panels and openings into surfaces that can be smoothed without creating pinching, seems, and surface distortion.
Sure they cover simply surfaces and show how to cut in support edges. But one quickly finds in "real world" models that these approaches are just not practical, unless you cut the entire model into smaller sections to localize the edges needs to cut openings, but then you are faced with trying to match panel / section edges that have different mesh densities.
Since nobody seems willing to share these techniques I am constantly trying to make up my own strategies to solve these surfacing problems in maya, that are handled quite easily in more sophisticated surfacing applications like rhino, solid works, inventor, alias auto, etc..
Example: Look at the top of the horizontal stabalizer (the tail)! Most of those edges are required just to make the upper corner of where the rudder is cut out tight! Also, notice the diagonal edges that have to radiate to the back of the rudder in order to spread the edges out to prevent seems! if you look closely at where I cut out the trim tabs in the elevator there is a seem and pinching and after spending nearly two hours trying I can only minimize it but not completely remove it.
Trying to average verts completely borks hard surface edge flow so it is not an option and god forbid you try to use maya's incredibly bad sculpt surface tool - which I contend should be renamed the "lumpy bumpy **** up your surface beyond all recognition tool", which is probably to long a name but more accurately describes what it does!
"If I have seen further it is by standing on the shoulders of giants." Sir Isaac Newton, 1675
Last edited by ctbram; 25-06-2011 at 05:03 PM.